Case Study Emmi
Container Refurbishing at Emmi in Dagmersellen
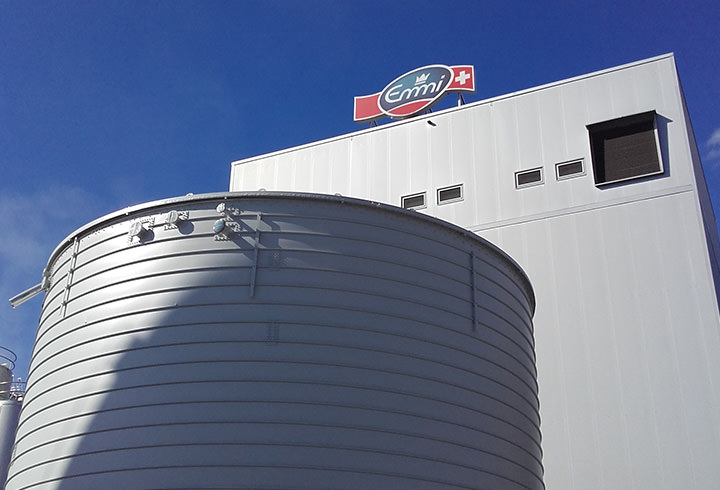
Sector
Food Industry
Application
Wastewater treatment
Product
1 x LIPP Buffer Tank
Year of construction
2016
Location
Dagmersellen, Switzerland
Summary
Refurbishing of a buffer tank for industrial sewage treatment under special circumstances at the Swiss milk processor Emmi in Dagmersellen.
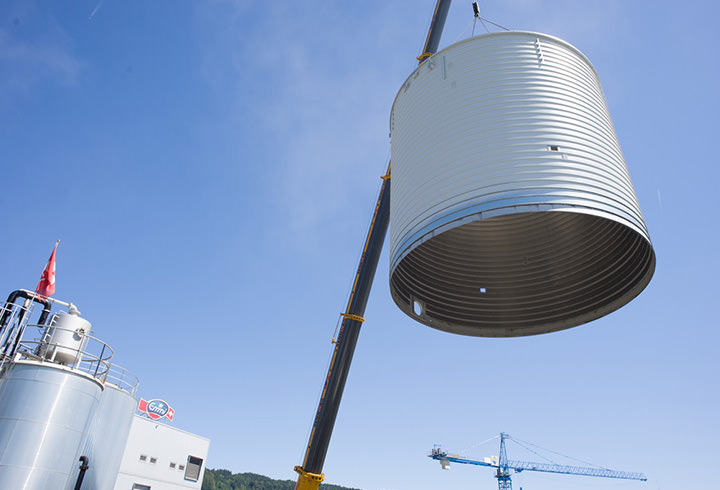
- Professional coordination with the client
- Tight schedule of 10 days for exchange the tanks
- Assembly of the new tank during operation
- Reduction of irrelevant piping of the old tank
- Remove the old tank
- Insert the new tank
- Re-installation of pipes and platforms
- Long-term experience and professionalism saved time and money
Initial Situation and solution searching
In a Swiss company, called Emmi, which is specialist in producing of milk powder and cream cheese, a tank should be exchanged at the plant’s internal waste water treatment plant.
This was, amongst others, a challenging task because it had to be ensured that the corroded container should be out of operation for a maximum of 10 days. This strict timetable had to be adhered to, otherwise the biology of the sewage treatment plant would have been destroyed and thus the load on the subsequent sewage treatment plant would have become much too much.
There were lots of meetings and visits at Emmi. At these meetings it had been determined that a pipe diversion of this important buffer storage tank has to be built at first, so the tank could be taken out of operation for these few days without disturbing the clarification operation.
The planning of this diversion was made more difficult by the fact that no design drawings or pipeline plans were available.
The first approach of a solution was a lining of the tank’s inner side, which would have been very complex, however, since the HdPE panels had to be glued to the entire inner side and the seams should be welded afterwards.
This is the big advantage of a LIPP container. Steel coils, machines and accessories are transported to the building site where the tank is then constructed – the process is fast, efficient and flexible.
The awarded duplex material VERINOX, developed by Lipp, combines stainless steel and a galvanized sheet with the aid of a separating layer. Thus, the outer side of the container is made of galvanized sheet metal and the inner side is made of stainless steel. Since stainless steel is very expensive, only a small amount is needed here, so costs will be saved and the quality of the medium side will be guaranteed.
However, Emmi decided instead to remove the old container and build a new container. The main reason was the cost savings due to the decommissioning of the buffer storage tank for only 10 days. Lipp GmbH was entrusted with this task.
Implementation of the solution
The old tank, which was surrounded by several tanks and buildings, had to be lifted carefully with a crane and a new LIPP Tank should be inserted.
The project process, including the production of the tank, the planning and organization and the coordination of the assembly schedule with the customer, was discussed on site.
Construction process
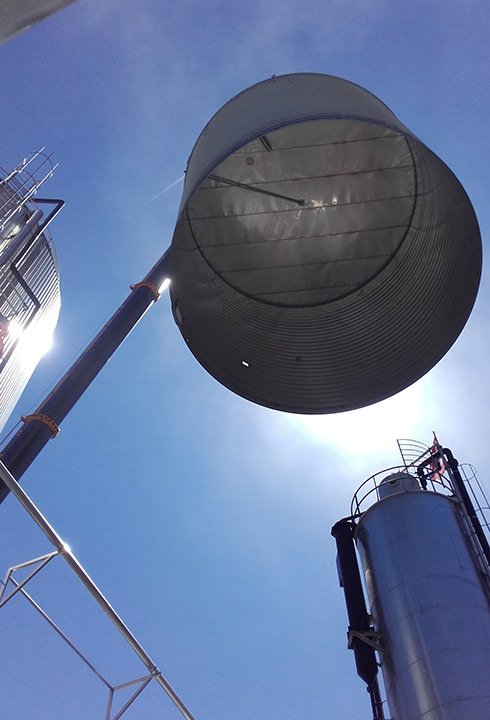
- New tank was built next door – everything necessary was prepared. New tank must be the same as the old one, just the material changed from 1.4301 to 1.4571
- Old tank was prepared for tank exchange. All irrelevant pipes and fittings of the old tank were dismantled within 5 days
- The exchange of tanks must took place on a Saturday as the internal operation is the least on Saturdays. The exchange had to be carried out very carefully, because no sensors, pipes and slides of the surrounding tanks couldn’t be damaged
- Old tank must be lifted with a crane. The cover was endangered by the corrosion, so the cover could only be entered with a fall protection to protect the Lipp employees
- Old floor has to be removed and the crane lifted the new floor. This new floor consists of a stainless steel membrane, like the LIPP stainless steel diaphragm roof cover
- The crane lifted the new tank
- Piping must be reassembled – after the new tank was successfully put down, the pipes, brackets, platforms, ladders and feeders were installed again – this must take place within 5 days
- The recommissioning took place
- Remaining work and removal of the old tank must be done in the parking area next to the building site. The old tank was put into the machine ring and was dismantled within 3 – 4 days