Case Study Fürth
New construction of a LIPP Gas Accumulator with 4,000 m³
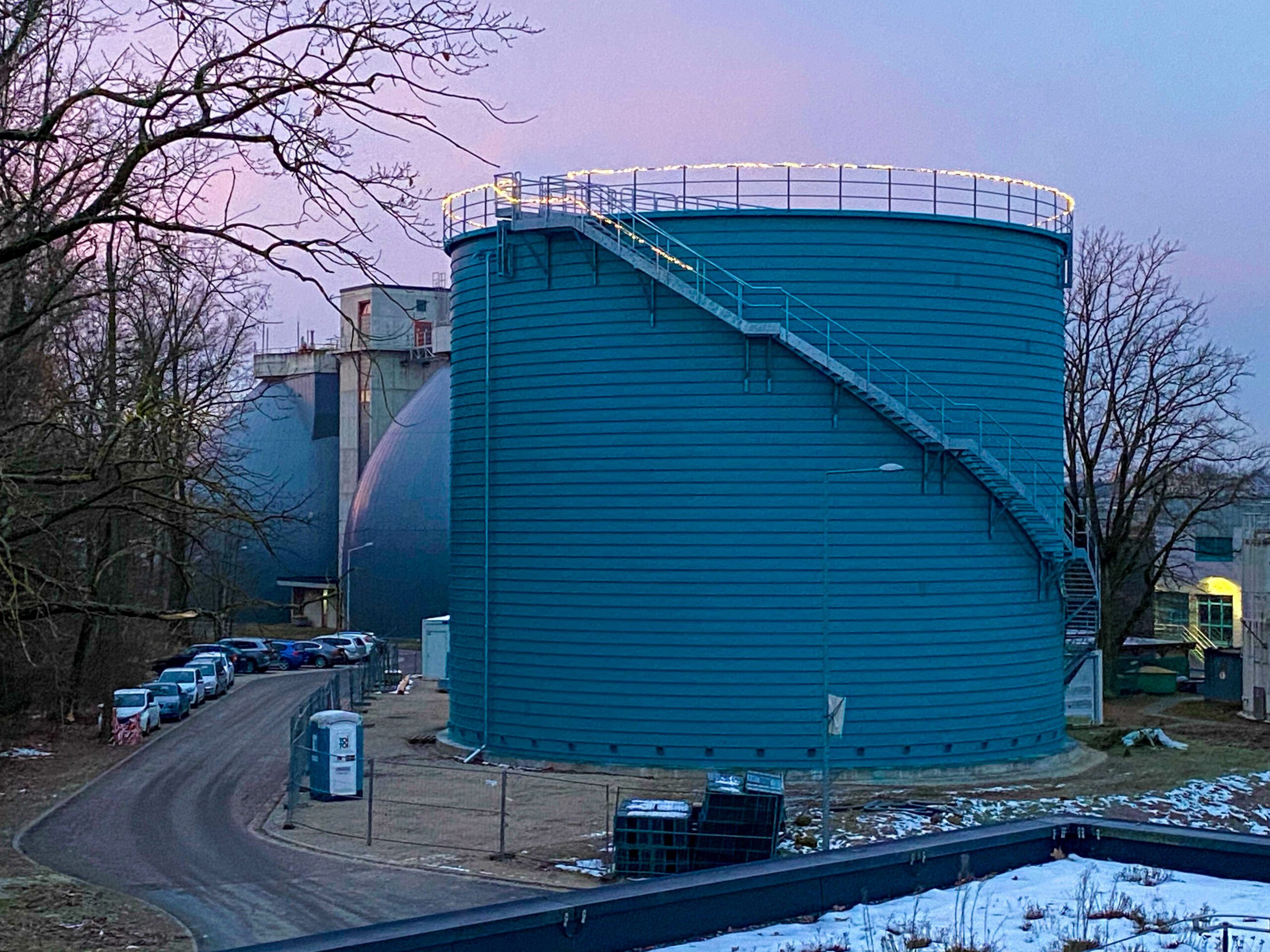
Sector
Municipalities
Application
Sewage gas storage
Product
1x LIPP Gas Accumulator
Year of construction
2023/2024
Location
Fürth, Deutschland
Summary
Construction of a new sewage gas storage facility to compensate for fluctuations in sewage gas production
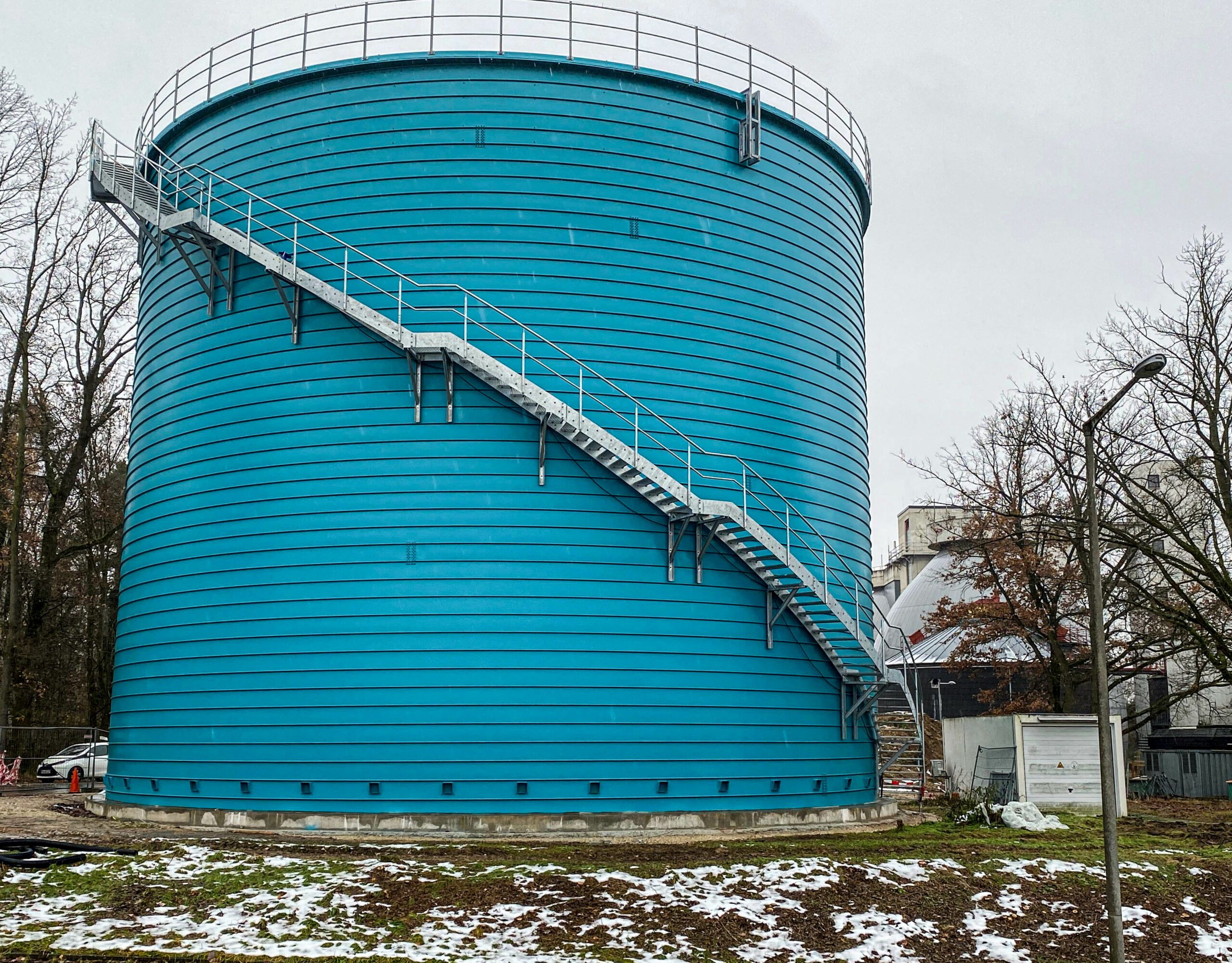
- Construction of a new LIPP Gas Accumulator with 4,000 m³ at the Fürth sewage treatment plant
- Stainless steel membrane roof with a diameter of 20 m
- On-site assembly with LIPP double seam system
- Quick realisation and low maintenance, with a long service life
Conversion of the Fürth sewage treatment plant
Stadtentwässerung Fürth (StEF) built a new sewage gas tank with a volume of 4,000 m³ on the site of the main sewage treatment plant in Fürth. The existing sewage gas tank had a volume of 800 m³, it was built in 1989 and was too small to compensate for the fluctuations in sewage gas production and electricity demand during the day. At the wastewater treatment plant in Fürth, approx. 6,000 m³ of sewage gas is produced daily during the sludge treatment associated with wastewater treatment. The LIPP Gas Accumulator facility was built between October 2023 and February 2024 and has a diameter of 20 metres and a height of 16 metres. With these gigantic dimensions, it has a storage volume of 4,000 m³ and is the largest LIPP Gas Accumulator ever built. The gas storage facility consists of two parts, a bubble-shaped storage balloon and a steel container that protects it from mechanical and weather influences. The steel tank was constructed using the patented LIPP double-seam system, and the tank is closed off by the stainless steel membrane roof, which is fully accessible. With the new LIPP Gas Accumulator, the proportion of self-generated electricity in the total electricity requirements of the sewage treatment plant can now be further increased. It also avoids the need to flare sewage gas on the one hand and to draw electricity from the grid or natural gas during the day on the other.